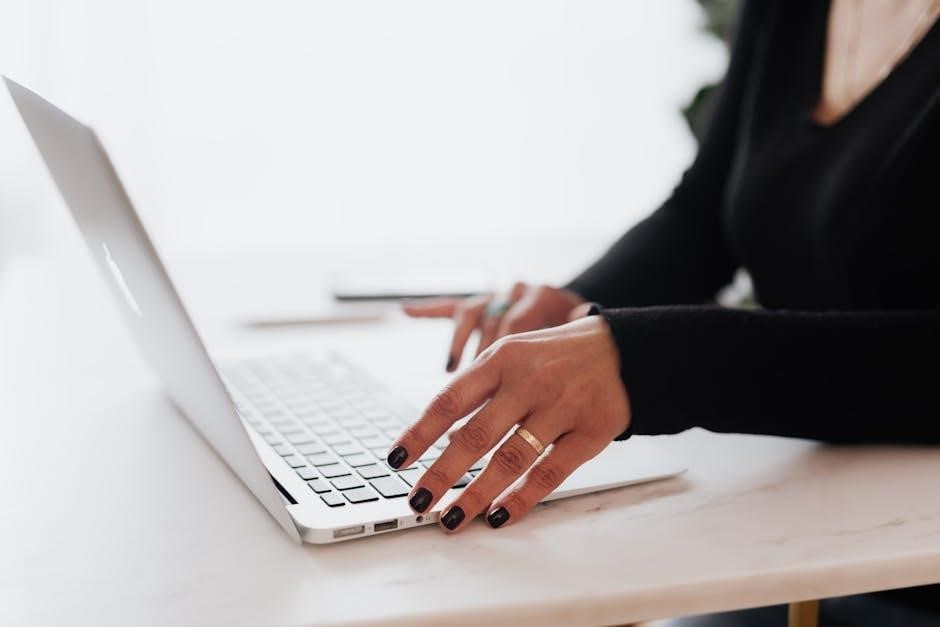
The Copeland Scroll Digital Compressor Controller is a advanced system designed to optimize performance and efficiency in HVAC applications. It provides precise control over compressor operation‚ ensuring reliable and energy-efficient cooling solutions. This manual serves as a comprehensive guide for technicians and system designers‚ covering installation‚ operation‚ and troubleshooting. By integrating seamlessly with Copeland Scroll compressors‚ it enables variable capacity modulation and advanced protection features‚ ensuring optimal performance and extended equipment lifespan.
1.1 Overview of the Controller and Its Importance
The Copeland Scroll Digital Compressor Controller is a cutting-edge digital interface designed to integrate seamlessly with Copeland Scroll compressors. It plays a crucial role in optimizing system performance by providing precise control over compressor operation. The controller is essential for managing variable capacity modulation‚ ensuring energy efficiency‚ and protecting the compressor from potential faults. Its advanced features‚ such as real-time monitoring and communication capabilities‚ make it indispensable for modern HVAC systems. This controller is a key component in achieving reliable and adaptable cooling solutions‚ tailored to meet the demands of various applications.
1.2 Historical Development of Copeland Scroll Technology
The Copeland Scroll compressor technology was first introduced in the 1980s‚ revolutionizing the HVAC industry with its innovative design. Initially‚ the scroll compressor offered improved reliability and efficiency compared to traditional compressors. Over time‚ Emerson Climate Technologies enhanced the technology‚ leading to the development of the digital scroll compressor. The integration of digital controls marked a significant milestone‚ enabling precise capacity modulation and advanced fault protection. This evolution has solidified the Copeland Scroll Digital Compressor Controller as a cornerstone of modern refrigeration systems‚ building on decades of innovation and industry leadership.
1.3 Purpose of the Manual and Target Audience
This manual is designed to provide detailed guidance for the installation‚ operation‚ and maintenance of the Copeland Scroll Digital Compressor Controller. It serves as an essential resource for HVAC technicians‚ system designers‚ and facility managers. The manual ensures that users can maximize the controller’s efficiency and performance. By covering technical specifications‚ troubleshooting‚ and best practices‚ it empowers professionals to handle complex tasks confidently. Whether for initial setup or ongoing maintenance‚ this guide is tailored to support all stakeholders involved in the system’s lifecycle‚ ensuring optimal functionality and longevity of the equipment.
Key Features of the Copeland Scroll Digital Compressor Controller
The controller offers variable capacity modulation‚ digital interface‚ and advanced energy efficiency. It includes protective faults‚ automatic reset‚ and seamless system integration‚ ensuring optimal performance and reliability always.
2.1 Variable Capacity Modulation (10-100% Range)
The Copeland Scroll Digital Compressor Controller features variable capacity modulation‚ allowing the compressor to operate between 10% and 100% of its capacity. This wide range ensures precise cooling by adjusting output to meet exact system demands‚ enhancing energy efficiency and reducing operational wear. The modulation is achieved through advanced digital controls‚ enabling smooth transitions and maintaining consistent system performance. This feature is particularly beneficial in applications requiring fluctuating cooling loads‚ ensuring optimal comfort and energy savings without compromising reliability.
2.2 Digital Interface and System Integration Capabilities
The Copeland Scroll Digital Compressor Controller offers a robust digital interface‚ enabling seamless integration with building management systems (BMS) and other external controls. It supports standard communication protocols like Modbus‚ ensuring compatibility with various system architectures. The controller’s open-platform design allows for real-time data exchange‚ remote monitoring‚ and centralized control. With two semiconductor outputs and compatibility with R-410A refrigerants‚ it adapts to diverse applications. Its intuitive interface simplifies setup and operation‚ while advanced connectivity options enhance system flexibility and scalability‚ making it ideal for modern HVAC and refrigeration systems.
2.3 Energy Efficiency and Performance Optimization
The Copeland Scroll Digital Compressor Controller excels in energy efficiency and performance optimization through advanced algorithms that adapt to varying load demands. Its variable capacity modulation ensures the compressor operates at the exact required level‚ minimizing energy consumption. The controller’s digital interface enables real-time monitoring and precise adjustments‚ further enhancing efficiency. By integrating with building management systems‚ it optimizes system-wide performance and reduces operational costs. Adaptive control logic ensures consistent and reliable operation‚ making it a superior choice for energy-conscious applications in HVAC and refrigeration systems.
2.4 Protective Faults and Automatic Reset Features
The Copeland Scroll Digital Compressor Controller incorporates advanced protective fault mechanisms to ensure safe and reliable operation. It detects high-pressure‚ low-pressure‚ and other critical system faults‚ triggering automatic shutdown if necessary. The controller features automatic reset capabilities for certain faults‚ minimizing downtime and reducing the need for manual intervention. Protective faults requiring manual reset are clearly indicated‚ ensuring prompt resolution. These safeguards enhance system longevity‚ prevent damage‚ and maintain optimal performance under various operating conditions‚ making it a robust solution for demanding HVAC and refrigeration applications.
Technical Specifications of the Controller
The Copeland Scroll Digital Compressor Controller offers compatibility with R-410A refrigerants‚ supports up to two semiconductor outputs‚ operates on 24V AC‚ and features Modbus communication for seamless system integration.
3.1 Compatibility with R-410A and Other Refrigerants
The Copeland Scroll Digital Compressor Controller is fully compatible with R-410A refrigerants‚ a widely used‚ eco-friendly option. It also supports other refrigerants such as R-22 and R-32‚ ensuring versatility. The controller’s advanced design allows seamless integration with various refrigerant types‚ optimizing performance and efficiency; Its compatibility ensures reduced environmental impact while maintaining high operational standards. This feature makes it suitable for diverse HVAC applications‚ from residential to commercial systems‚ ensuring reliable operation across different refrigerant requirements.
3.2 Maximum Semiconductor Outputs (Up to 2 Outputs)
The Copeland Scroll Digital Compressor Controller supports up to two semiconductor outputs‚ enabling precise control of compressor operations. These outputs are designed for capacity modulation‚ allowing the compressor to adjust its performance based on system demands. This feature enhances energy efficiency and ensures smooth operation. The dual outputs provide flexibility for integrating with various HVAC systems‚ supporting both single and three-phase compressors. This capability ensures reliable performance and optimal system control‚ making it suitable for a wide range of applications. The outputs are critical for maintaining efficient and consistent cooling performance.
3.3 Operating Voltage and Power Requirements
The Copeland Scroll Digital Compressor Controller operates within a specified voltage range‚ ensuring compatibility with both single-phase and three-phase power systems. Its design optimizes energy efficiency‚ minimizing power consumption while maintaining high performance. The controller supports a wide range of operating voltages‚ making it versatile for various HVAC applications. Power requirements are carefully balanced to ensure reliable operation without excessive energy draw. This feature enhances overall system efficiency and stability‚ making it suitable for both residential and commercial environments. The controller’s power management capabilities are integral to its ability to deliver consistent and energy-efficient performance.
3.4 Communication Protocols and Connectivity Options
The Copeland Scroll Digital Compressor Controller supports a variety of communication protocols‚ including BACnet and Modbus‚ enabling seamless integration with Building Management Systems (BMS). These protocols facilitate data exchange‚ allowing real-time monitoring and control of compressor performance. The controller also offers remote monitoring and control capabilities through compatible software platforms. Its connectivity options ensure enhanced system coordination‚ improved diagnostics‚ and optimized performance. By leveraging these communication features‚ users can achieve greater operational efficiency and scalable system management‚ making it ideal for both standalone and networked applications. This versatility ensures compatibility with diverse HVAC system configurations and requirements.
Installation and Setup Guidelines
Proper installation ensures optimal performance and safety. Follow pre-installation checks‚ wiring guidelines‚ and initial configuration steps outlined in the manual; Ensure all electrical connections are secure and meet manufacturer specifications for reliable operation and efficiency.
4.1 Pre-Installation Checks and Requirements
Before installing the Copeland Scroll Digital Compressor Controller‚ ensure compatibility with the compressor model and refrigerant type‚ such as R-410A. Verify the power supply matches the controller’s voltage requirements and check all electrical connections for integrity. Ensure proper grounding to prevent electrical hazards and confirm the system’s operating conditions align with the controller’s specifications. Review the manual to ensure all safety precautions are understood. Validate the controller’s software version and update if necessary. Additionally‚ inspect the environment for temperature and humidity levels within acceptable ranges to ensure reliable operation and compliance with safety standards.
4.2 Step-by-Step Installation Process
Mount the controller securely on a flat surface near the compressor‚ ensuring proper ventilation. Connect the electrical wiring according to the diagram‚ matching terminals carefully. Attach the digital interface cable to the compressor and system controller. Set the controller’s operating mode and parameters using the digital interface. Initialize the compressor by following the startup sequence outlined in the manual. Test the system under load to verify proper operation and adjust settings as needed. Ensure all connections are secure and double-check wiring for accuracy before powering up. Follow the sequence to avoid errors and ensure safe startup.
4.3 Wiring and Electrical Connections
Ensure the power supply matches the controller’s voltage requirements. Connect the live‚ neutral‚ and ground wires to the designated terminals on the controller. Use appropriately sized wire gauges to prevent voltage drop. Refer to the wiring diagram in the manual for terminal connections. Connect the compressor’s electrical wires to the controller’s output terminals‚ ensuring correct phase alignment. Install a ground wire to prevent electrical noise and ensure safety. Double-check all connections for tightness and accuracy. Power up the system only after verifying all wiring is correct. Always disconnect power before making or adjusting connections. Follow local electrical codes and safety guidelines. Use protective gear when handling live circuits. Ensure proper insulation of all wires to prevent short circuits. Verify the controller’s communication ports are connected to the system interface if required. Test the electrical connections with a multimeter before initial startup. Ensure all wiring complies with the controller’s specifications and local regulations. Proper wiring ensures reliable operation‚ efficiency‚ and safety. Refer to the manual for specific wiring instructions tailored to your system configuration. Consult a licensed electrician if unsure about any connections. Regularly inspect wiring for signs of wear or damage to maintain optimal performance. Always follow the manufacturer’s guidelines for electrical connections to avoid voiding the warranty. Proper wiring is critical for the controller’s functionality and the overall system’s efficiency. Ensure all connections are secure and meet safety standards before commissioning the system. This ensures smooth operation and minimizes the risk of electrical faults. Compliance with wiring standards is essential for system reliability and safety. Always test the system thoroughly after completing the wiring to ensure proper functionality. This step is crucial for identifying and addressing any potential issues early. Proper wiring ensures the controller can accurately control and protect the compressor‚ maximizing efficiency and lifespan. Follow the manual’s instructions precisely to avoid errors during the wiring process. Electrical connections are the foundation of a reliable and efficient system‚ so attention to detail is critical. Ensure all wiring is neatly organized to prevent interference and simplify future maintenance. Secure all connections with appropriate fasteners to prevent vibration-related issues. Use high-quality connectors and cables to ensure durability and performance. Proper grounding is essential for noise reduction and safety. Verify that all ground wires are securely connected to a proper earth point. This ensures the system operates safely and efficiently. Always refer to the manual for specific wiring requirements‚ as incorrect connections can lead to system malfunctions. Electrical connections must be handled with care to prevent damage to the controller or compressor. Use tools rated for the task to avoid accidental short circuits. Ensure all wires are correctly labeled and color-coded for easy identification. This simplifies troubleshooting and future maintenance. Proper wiring practices ensure the controller functions as intended‚ providing precise control and protection for the compressor. Always double-check the wiring before powering up the system to ensure everything is connected correctly. This step is vital for preventing electrical faults and ensuring safe operation. Proper wiring ensures the controller can communicate effectively with the compressor and other system components. Follow the manual’s guidelines to ensure compatibility and proper signal transmission. Regularly inspect and maintain the wiring to prevent issues over time. This ensures the system continues to operate efficiently and reliably. Proper electrical connections are the backbone of a well-functioning HVAC system‚ so careful attention is necessary. Use the wiring diagram provided in the manual as a reference to ensure accuracy. Test each connection individually to confirm it is secure and functioning correctly. This ensures the system operates smoothly from the start. Proper wiring practices prevent electrical hazards and ensure the system meets safety standards. Always follow local regulations and manufacturer guidelines when making electrical connections. This ensures compliance and minimizes the risk of electrical faults. Proper wiring is essential for the controller to function correctly‚ so take the time to ensure all connections are accurate and secure. Refer to the manual for detailed instructions and troubleshooting tips if issues arise. Proper wiring ensures the controller can optimize compressor performance and efficiency. Always verify that all connections are correct before commissioning the system to ensure reliable operation. Proper electrical connections ensure the system operates safely‚ efficiently‚ and reliably‚ maximizing its performance and lifespan. Follow the manual’s wiring instructions carefully to achieve optimal results.
4.4 Initial Configuration and Parameter Setup
After installation‚ power up the controller and access the digital interface. Select the compressor type and refrigerant via the menu. Set operating parameters like temperature‚ pressure‚ and modulation range. Enable protective features such as high/low-pressure limits and current overload protection. Configure communication settings if integrating with a BMS. Test the system under load to ensure proper operation. Refer to the manual for default settings and customization options. Save all configurations before exiting. This step ensures the controller operates efficiently and safely‚ tailored to your system’s needs. Proper setup is critical for optimal performance and reliability.
Operating the Copeland Scroll Digital Compressor Controller
The Copeland Scroll Digital Compressor Controller operates by executing advanced control logic and algorithms‚ enabling real-time monitoring and adjustments through its digital interface and remote control capabilities‚ ensuring optimal performance and energy efficiency in HVAC systems.
5.1 Understanding the Control Logic and Algorithms
The Copeland Scroll Digital Compressor Controller uses sophisticated control logic and algorithms to regulate compressor operation based on system demands. These algorithms process inputs like temperature‚ pressure‚ and humidity to adjust capacity modulation between 10-100%. The controller executes precise control over the compressor’s digital valves and unloading mechanisms‚ ensuring optimal performance. Advanced fault detection and protective mechanisms are integrated to prevent operational anomalies. Real-time monitoring and adjustments are enabled through the digital interface‚ allowing for efficient system management and energy savings. This ensures the compressor operates smoothly‚ efficiently‚ and reliably in various applications.
5.2 Monitoring and Adjusting Compressor Performance
The Copeland Scroll Digital Compressor Controller offers real-time monitoring of compressor performance through its digital interface. Users can track key parameters such as temperature‚ pressure‚ and compressor speed. The controller automatically adjusts compressor capacity to match system demands‚ ensuring efficient operation. Manual adjustments can be made via the interface to fine-tune performance. The system provides alerts for deviations from setpoints‚ enabling proactive maintenance. This continuous monitoring and adjustment capability ensures optimal efficiency‚ reduced wear on components‚ and consistent cooling performance‚ making it an essential tool for maintaining system reliability and energy savings. Regular checks and adjustments are recommended to maintain peak performance levels.
5.3 Using the Digital Interface for Real-Time Data
The Copeland Scroll Digital Compressor Controller features a user-friendly digital interface that provides real-time data on system performance. This interface displays critical parameters such as temperature‚ pressure‚ and compressor speed‚ enabling precise monitoring. Operators can access historical data and performance trends to identify patterns and optimize settings. The digital interface also supports remote monitoring‚ allowing users to track system status from a centralized location. This real-time data capability enhances diagnostic accuracy and enables proactive adjustments‚ ensuring efficient operation and minimizing downtime. The interface is compatible with various communication protocols‚ making it easy to integrate with building management systems for comprehensive control. By leveraging this data‚ users can make informed decisions to maintain optimal performance and energy efficiency. Regular reviews of real-time data are essential for maximizing system reliability and longevity.
5.4 Remote Monitoring and Control Options
The Copeland Scroll Digital Compressor Controller offers robust remote monitoring and control capabilities‚ enabling users to manage system performance from a centralized location. Through communication protocols such as Modbus or BACnet‚ the controller can integrate with building management systems (BMS) or dedicated software platforms. This allows for real-time monitoring of operational parameters‚ performance adjustments‚ and fault detection. Remote access can be achieved via web or mobile interfaces‚ ensuring flexibility and responsiveness. These features reduce the need for on-site visits‚ enabling faster troubleshooting and minimizing downtime. Remote control options also support automated responses to system alerts‚ ensuring continuous operation and energy efficiency.
Troubleshooting Common Issues
The Copeland Scroll Digital Compressor Controller provides detailed fault codes and diagnostics to identify and resolve common operational issues efficiently. The manual offers step-by-step solutions for troubleshooting.
6.1 Identifying and Diagnosing Fault Codes
The Copeland Scroll Digital Compressor Controller features an advanced fault code system to help identify and diagnose operational issues. Fault codes are displayed through the digital interface or LED indicators‚ providing clear indicators of system malfunctions. Users can refer to the manual to interpret specific codes‚ such as Code 2 for high-pressure faults. The controller’s protection module logs errors‚ enabling technicians to trace the root cause of issues. By analyzing these codes‚ users can address problems promptly‚ ensuring minimal downtime and maintaining system efficiency. Regular reviews of fault codes are essential for proactive maintenance and troubleshooting.
6.2 Common Operational Issues and Solutions
Common operational issues with the Copeland Scroll Digital Compressor Controller include incorrect wiring‚ sensor malfunctions‚ and communication errors. If the controller fails to communicate with the compressor‚ check wiring connections and ensure all terminals are secure. Sensor issues may require recalibration or replacement. For communication faults‚ verify protocol settings and restart the system. Additionally‚ low refrigerant levels or high-pressure imbalances can trigger protective shutdowns; Addressing these issues promptly helps maintain system performance and prevents further complications. Always consult the manual for specific troubleshooting steps and solutions to ensure optimal operation. Regular system checks can prevent these issues from arising.
6.3 Resetting the Controller and Clearing Faults
To reset the Copeland Scroll Digital Compressor Controller‚ first power cycle the unit by disconnecting and reconnecting the power supply. This often resolves temporary glitches. For manual reset‚ press and hold the reset button for 5 seconds while the controller is powered on. If faults persist‚ check the fault codes displayed on the interface and refer to the manual for specific solutions. Some faults may require manual intervention‚ such as addressing high-pressure thresholds or communication errors. After clearing faults‚ test the system to ensure proper operation. Always consult the manual for detailed reset procedures. Regular resets can prevent system downtime.
6.4 Advanced Diagnostic Techniques
Advanced diagnostics involve analyzing system logs‚ pressure readings‚ and communication data; Use the digital interface to review historical fault codes and performance trends. Check for pressure imbalances and verify sensor accuracy. Ensure proper communication between the controller and system components. Utilize specialized tools‚ such as Emerson’s EC2 controller diagnostics‚ to identify deep-rooted issues. Refer to the manual for detailed procedures on resetting fault conditions and recalibrating sensors. Regularly updating the controller’s firmware ensures optimal performance and addresses potential bugs. Always follow safety protocols when performing advanced diagnostics to avoid system damage or personal injury.
Maintenance and Service Recommendations
Regular maintenance ensures optimal performance and longevity. Schedule tasks like filter cleaning‚ software updates‚ and sensor calibration. Replace wearable parts promptly to prevent system failures.
7.1 Scheduled Maintenance Tasks
Regular maintenance is crucial for optimal performance. Schedule daily checks of filter cleanliness and refrigerant levels. Weekly‚ inspect electrical connections and sensor accuracy. Monthly‚ review system logs and perform software updates. Every 6 months‚ clean condenser coils and check compressor alignment. Annual maintenance should include replacing wearable parts and performing a full system calibration. Always follow manufacturer guidelines and ensure tasks are performed by qualified personnel. Adherence to these schedules ensures reliability‚ efficiency‚ and extends the lifespan of the controller and compressor system. Proper documentation of maintenance activities is also recommended for tracking and future reference.
7.2 Calibration and Update Procedures
Calibration ensures the controller operates accurately with the compressor. Begin by downloading the latest software updates from the manufacturer’s website. Connect the controller to a PC via USB or direct communication link. Run the update utility‚ following on-screen instructions to install new firmware. After updating‚ recalibrate sensors and verify settings match system requirements. Regular updates maintain compatibility and improve performance. Always refer to the manual for specific calibration steps. Updates should only be performed by authorized personnel to prevent system malfunctions. Proper documentation of updates ensures traceability and compliance with maintenance standards.
7.3 Replacement of Wearable Parts
Regular inspection and replacement of wearable parts ensure optimal performance and prevent premature system failure. Identify parts requiring replacement‚ such as contactors‚ relays‚ and sensors‚ by consulting the manual or manufacturer guidelines. Always disconnect power and discharge capacitors before starting work. Use genuine Copeland replacement parts to maintain compatibility and performance. Replace worn or damaged components carefully‚ following torque specifications and electrical connections. After replacement‚ test the system to ensure proper operation. Document all replacements for future reference and schedule regular inspections to maintain system reliability and efficiency.
7.4 Best Practices for Longevity and Efficiency
Regular maintenance‚ proper installation‚ and adherence to manufacturer guidelines are crucial for maximizing the lifespan and efficiency of the Copeland Scroll Digital Compressor Controller. Ensure all electrical connections are secure and clean‚ and maintain proper refrigerant levels to prevent system strain. Schedule periodic calibration of sensors and controls to ensure accurate operation. Keep the controller and surrounding areas free from debris to promote airflow and heat dissipation. Document all maintenance activities and performance data for trend analysis. Train personnel on proper operation and troubleshooting to minimize misuse. By following these practices‚ you can ensure optimal performance‚ reduce downtime‚ and extend the controller’s service life.
Integration with Building Management Systems (BMS)
The Copeland Scroll Digital Compressor Controller seamlessly integrates with popular BMS platforms‚ enabling real-time monitoring and control of HVAC systems. Its communication protocols ensure efficient data exchange‚ optimizing system performance and energy use while providing centralized management capabilities for enhanced operational control and decision-making.
8.1 Compatibility with Popular BMS Platforms
The Copeland Scroll Digital Compressor Controller is designed to integrate smoothly with leading Building Management Systems like Siemens Desigo‚ Johnson Controls Metasys‚ and Honeywell Enterprise Buildings Integrator. Its open communication protocols‚ including BACnet and Modbus‚ ensure seamless connectivity and data exchange. This compatibility allows for centralized monitoring and control‚ enabling facility managers to optimize energy efficiency‚ track performance metrics‚ and receive real-time alerts. The controller’s flexible architecture supports customized integration‚ making it adaptable to various building automation systems‚ thus enhancing overall system functionality and user experience through unified control.
8.2 Data Exchange and Communication Protocols
The Copeland Scroll Digital Compressor Controller supports various communication protocols‚ including BACnet‚ Modbus‚ and LonWorks‚ enabling seamless data exchange with building management systems. These protocols allow real-time monitoring of compressor performance‚ temperature‚ and pressure‚ ensuring precise control and efficient system management. The controller’s ability to integrate with these standards facilitates centralized monitoring‚ reducing operational complexity. By leveraging these communication protocols‚ users can achieve enhanced system scalability and adaptability‚ ensuring optimal performance across diverse applications and environments.
8.3 Custom Integration Solutions
The Copeland Scroll Digital Compressor Controller offers customizable integration solutions to meet specific system requirements. It supports tailored control algorithms and communication protocols‚ ensuring compatibility with diverse building management systems. Users can configure the controller to manage multiple compressor lines with different types‚ enhancing system flexibility. Custom integration allows for precise control of compressor operation‚ optimizing performance for unique applications. This adaptability ensures the controller can be fine-tuned to deliver maximum efficiency and reliability in various HVAC setups‚ making it a versatile choice for complex systems.
8.4 Benefits of BMS Integration
Integrating the Copeland Scroll Digital Compressor Controller with a Building Management System (BMS) enhances overall system efficiency and control. It enables centralized monitoring and management of HVAC operations‚ providing real-time data access for informed decision-making. Energy consumption is optimized through precise control of compressor performance‚ reducing operational costs. Remote monitoring and control capabilities improve responsiveness to system changes. Enhanced diagnostics and fault detection ensure proactive maintenance‚ minimizing downtime. Scalability and adaptability to various system sizes make it ideal for both small and large applications‚ ensuring a seamless and efficient HVAC solution tailored to specific needs.
Safety and Protective Features
The Copeland Scroll Digital Compressor Controller features built-in safety mechanisms‚ including high-pressure and low-pressure safeguards‚ emergency shutdown procedures‚ and protective faults requiring manual reset for enhanced reliability and operator safety.
9.1 Built-In Safety Mechanisms
The Copeland Scroll Digital Compressor Controller incorporates advanced safety mechanisms to protect the compressor and system. These include automatic shutdown in case of high or low-pressure thresholds‚ thermal protection‚ and fault detection. The controller continuously monitors operational parameters‚ ensuring safe operation by preventing overheating‚ overloading‚ or other potential hazards. Built-in safeguards also prevent compressor damage during startup or shutdown cycles. These mechanisms enhance reliability‚ reduce downtime‚ and ensure compliance with safety standards‚ providing peace of mind for operators and extending the lifespan of the equipment.
9.2 Protective Faults Requiring Manual Reset
The Copeland Scroll Digital Compressor Controller includes protective faults that require manual reset to ensure safe operation. These faults are triggered by critical conditions‚ such as high discharge pressure‚ low suction pressure‚ or overheating. Once a fault occurs‚ the controller shuts down the compressor and displays an error code. Manual reset is necessary to restart operation‚ allowing technicians to address the underlying issue. This feature prevents potential damage to the compressor or system‚ ensuring reliability and safety. The manual provides detailed fault codes and procedures for resetting‚ enabling quick troubleshooting and maintenance. This enhances system uptime and operational integrity.
9.3 High-Pressure and Low-Pressure Safeguards
The Copeland Scroll Digital Compressor Controller incorporates high-pressure and low-pressure safeguards to protect the system from operational extremes. These safeguards monitor pressure levels and activate protective measures if thresholds are exceeded. For instance‚ high-discharge pressure or low-suction pressure triggers the controller to shut down the compressor and display an error code. This prevents potential damage to the compressor and ensures safe operation. The controller’s advanced algorithms continuously monitor pressure fluctuations‚ providing reliable protection against extreme conditions. These features enhance system reliability and longevity‚ ensuring optimal performance without compromising safety. Regular monitoring of these safeguards is crucial for maintaining operational integrity.
9.4 Emergency Shutdown Procedures
The Copeland Scroll Digital Compressor Controller includes emergency shutdown procedures to immediately halt operation in critical situations. These procedures are triggered by severe deviations in pressure‚ temperature‚ or system faults. Upon activation‚ the controller disables the compressor and associated components‚ ensuring safety. An audible or visual alarm may signal the shutdown‚ depending on system configuration. The compressor remains inactive until the issue is resolved and a manual reset is performed. These procedures are designed to protect both the equipment and operators from potential hazards‚ ensuring a safe and controlled shutdown process in emergencies. Regular testing of these protocols is recommended to maintain reliability.
10.4 Training and Operator Competence
Best Practices for Optimal Performance
Regular maintenance‚ performance monitoring‚ and proper system integration ensure optimal operation. Training operators and following manufacturer guidelines further enhance efficiency and reliability of the Copeland Scroll Digital Compressor Controller.